鎂碳磚是日本作為電爐應(yīng)用而開發(fā)的,首次應(yīng)用在轉(zhuǎn)爐鎂碳磚價格的實驗在1970年開始的,經(jīng)過6年正式推廣使用,1977年川崎鋼鐵公司在轉(zhuǎn)爐爐底和風(fēng)口首次使用樹脂結(jié)合的鎂碳磚,開創(chuàng)了含石墨的復(fù)合耐火材料在轉(zhuǎn)爐應(yīng)用的先例。瀝青結(jié)合的鎂碳磚由西歐興起的,通常的鎂碳磚是有鎂砂和鱗片狀石墨中作為結(jié)合劑添加了熱固性樹脂,加入或不加防氧化劑的不燒磚。近幾十年來,由于日益苛刻的冶煉條件和不斷變化鋼鐵冶煉生產(chǎn)技術(shù),對鎂碳質(zhì)耐火材料提出了較高的要求,主要集中在改進工藝,提高質(zhì)量和使用效果,并已取得了良好效果。下文是鎂碳磚原材料的選擇,供參考!
為驗證該防氧化涂料的實際使用效果,我們在三個鋼廠分別進行了現(xiàn)場試驗。采用鋼包渣線鎂碳磚的局部涂刷和侵蝕最嚴(yán)重處的整體涂刷兩種方式,來評價防氧化涂料起到的作用。局部涂刷的現(xiàn)場,觀察鋼包烘烤結(jié)束后渣線鎂碳磚的外觀,測量鋼包下線后涂刷部分的殘余厚度,對比未涂刷涂料且與涂刷涂料部分處在相同使用環(huán)境的渣線鎂碳磚殘余厚度(結(jié)果見圖4和圖5)。侵蝕最嚴(yán)重處整體涂刷的現(xiàn)場,新砌鋼包烘烤時間為120小時,高烘烤溫度1000℃,選定侵蝕最嚴(yán)重的部位作為研究對象,對比涂刷前后該處鎂碳磚殘余厚度和使用壽命。
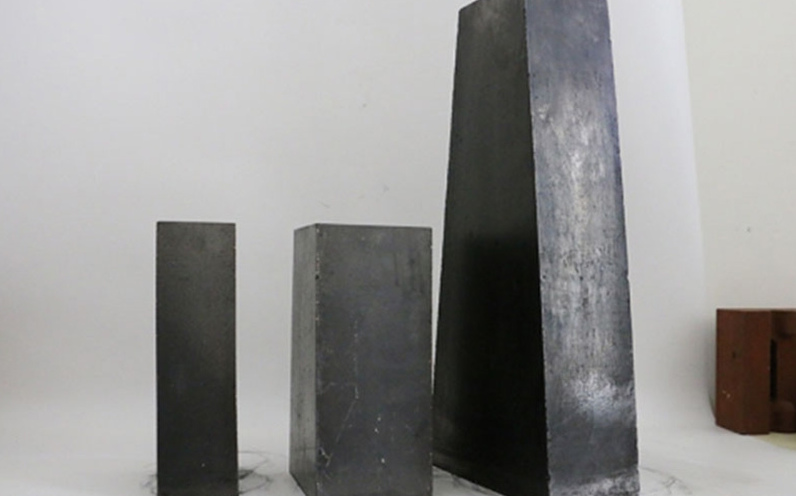
出了不同碳源對試樣經(jīng)不同溫度處理后常溫耐壓強度的影響。可以看出,與200℃熱處理后各試樣的常溫耐壓強度相比,經(jīng)埋碳保溫處理后,其他溫度處理后試樣A1、A2、A3的耐壓強度都出現(xiàn)大幅度降低,隨著溫度的提高,各鎂碳磚試樣的耐壓強度又逐漸有所升高。這是由于酚醛樹脂在200℃時固化,此時主要靠樹脂本身提供強度。但在熱處理過程中,樹脂發(fā)生分解,釋放H2O、CH4、CO2等氣體,氣體的大量揮發(fā)會產(chǎn)生氣孔,導(dǎo)致試樣的顯氣孔率增大,致密度下降,強度下降。此時試樣強度的大小由樹脂殘?zhí)己吞克卦纤纬傻奶冀Y(jié)構(gòu)所決定。但溫度為1200及1400℃時,基質(zhì)會發(fā)生燒結(jié)使試樣致密度提高,試樣的顯氣孔率也出現(xiàn)下降,強度隨之開始升高。在經(jīng)過埋碳熱處理后,試樣A3均具有高強度,這主要和瀝青本身具有黏結(jié)作用有關(guān)。鎂碳磚廠家
各試樣高溫抗折試驗后試樣基質(zhì)的XRD圖譜見圖4。由圖4可知:3個試樣中均含有方鎂石、鎂橄欖石以及少量的Si C和C。高溫抗折試驗后試樣斷面的顯微結(jié)構(gòu)照片見圖5。可以看到:試樣A1中生成較多發(fā)育良好的柱狀晶體,根據(jù)物相組成并結(jié)合微區(qū)成分分析判斷是鎂橄欖石,還有一些空心管狀物,根據(jù)文獻可以判斷主要是樹脂裂解生成的碳管或碳洋蔥,粒狀晶體為碳化硅;試樣A2中存在較多棒槌狀晶體,根據(jù)物相組成和結(jié)合微區(qū)成分分析,判斷主要是發(fā)育不完全的鎂橄欖石,管狀物為碳管或納米碳管,粒狀晶體為碳化硅;而試樣A3同時存在著大量的長度較長的發(fā)育不完全的鎂橄欖石及碳管或納米碳管,值得注意的是還有數(shù)量較多的Si C纖維生成,可以推斷是由液-氣或固-氣反應(yīng)形成;而試樣A1、A2中未見纖維狀Si C,而呈粒狀,可以推斷是由液-固或固-固反應(yīng)形成。鎂碳磚