目前鋼包使用的工作襯,尤其是渣鎂碳磚廠家線部位多采用含碳耐火材料。新砌筑好的鋼包,在投入盛裝鋼水使用前,須預先按照從小火、中火到大火的順序進行烘烤,一般烘烤溫度達到1000℃左右,整個烘烤過程,時間短的需要20-30小時,長則需要3-5天,有的甚至更長。目前,相當多的鋼包使用現(xiàn)場并沒有采取針對烘烤過程中含碳工作襯的防氧化措施,導致烘烤完畢待用時,工作層鎂碳磚已經(jīng)產(chǎn)生至少20mm左右的氧化脫碳層;也有少部分的鋼包工作層鎂碳磚在砌筑后涂刷防氧化涂料,但是防氧化效果并不能達到理想的效果。另外,涂料需要在現(xiàn)場加水調(diào)配,使用不方便,導致了大多數(shù)鋼包使用現(xiàn)場放棄了采用防氧化涂料。為此,我們研發(fā)了一種預先調(diào)配好的、方便使用的新型防氧化涂料,并對其防氧化效果進行了相關試驗。
烘包結(jié)束后,沒有涂刷涂料的爐襯外觀已經(jīng)被氧化而變色,用鋼管輕輕一捅,鎂碳磚的脫碳層便脫落;而涂刷涂料的部分表面,涂料已經(jīng)形成密致保護層,且保護層分布均勻,與鎂碳磚結(jié)合緊密,沒有脫落現(xiàn)象,說明涂刷起到了良好的防氧化效果。圖5是鋼包下線后的照片。經(jīng)測量殘余鎂碳磚厚度,涂刷涂料的鎂碳磚使用下線后殘余厚度約100mm,相同使用條件下未涂刷涂料鎂碳磚的殘余厚度約為75mm,涂刷涂料的殘厚比不涂刷的殘厚多25mm左右。
侵蝕最嚴重處整體涂刷的現(xiàn)場,鋼包涂刷前后對比照片見圖6。從圖6可以開出,未涂涂料時,鋼包烘烤后,由于長時間的烘烤,鎂碳磚氧化嚴重,氧化層松散,幾乎沒有強度;而涂刷涂料的鎂碳磚烘烤后表面仍為黑色,且強度仍然很高,沒有松散現(xiàn)象。鋼包下線后,侵蝕最嚴重的幾環(huán)處的殘余厚度明顯比涂刷前高出很多。渣線未涂刷涂料前,渣線鎂碳磚使用壽命為28-32次,侵蝕最嚴重部位鎂碳磚的殘余厚度為80mm左右。渣線整體涂刷涂料后,渣線鎂碳磚使用壽命為29次(因為透氣磚而下線),侵蝕最嚴重部位鎂碳磚的殘余厚度為120mm,說明涂料保護了之前因為長時間烘烤而氧化的40mm的鎂碳磚。
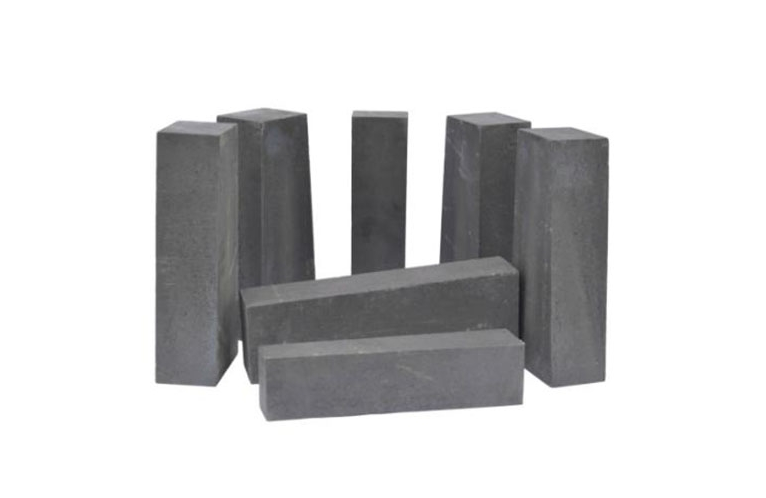
鎂碳磚的損毀過程:鎂碳磚的損毀,首先是由于磚內(nèi)的碳氧化,形成脫碳層,加之高溫下氧化鎂與石墨的熱膨脹率相差懸殊(1000℃時分別為1.4%和0.2%),導致組織結(jié)構(gòu)疏松,強度降低,再經(jīng)熔渣的侵蝕、機械沖刷等作用,磚中的氧化鎂顆粒逐漸被熔蝕,逐層脫落,從而造成鎂碳磚的損毀。鎂碳磚的損毀過程是:氧化→脫碳→疏松→侵蝕→沖刷→脫落→損毀。大量的研究工作證明,1600℃以上,如下反應是導致鎂碳磚損毀的主要原因。鎂碳磚價格
MgO(s)+C(s)→Mg(g)+CO(g) (1)
鎂碳磚的損毀,首先是工作襯熱面中的碳氧化,形成一層薄的脫碳層,碳的氧化是由于不斷被爐渣中鐵的氧化物和空氣中的O?以及CO?、SiO?等氧化物氧化的結(jié)果,以及溶解于鋼液之中或磚中的MgO對碳的汽化作用;其次是高溫液態(tài)熔渣滲入脫碳層的氣孔或由于熱力的作用產(chǎn)生的裂紋之中,與磚中的氧化鎂反應形成低熔點的化合物,致使磚的表面層發(fā)生質(zhì)變并弱化,在強大的鋼渣攪動、機械沖刷等應力作用下逐層脫落,導致鎂碳磚的損毀,如此周而復始,爐襯逐層變薄,最終補爐、修爐、停爐。
添加防氧化劑碳化硼的試樣,其中的碳化硼優(yōu)先C被氧化,而使材料內(nèi)部氧氣分壓PO2大大降低,這就保護了C不被大量的氧化;同時,碳化硼氧化后,生成液相B2O3,在試樣表面形成一層液膜,阻塞材料氣孔,降低O2在試樣表面的擴散速率,從而降低C的氧化程度;另外,液體B2O3對MgO具有較好的潤濕性,兩者很容易反應生成硼酸三鎂(3MgO·B2O3),而硼酸三鎂可以形成致密的保護層,能進一步封閉鎂碳磚表面的氣孔,阻礙O2的侵入,從而保護C的氧化碳化硼通過上述途徑防止鎂碳磚中C的氧化,降低高溫下的C氧化留下的氣孔,加強高溫下的固-固結(jié)合,從而提高鎂碳磚的高溫抗折強度。遼寧鎂碳磚